Flexible
film turns heat to power
By
Chhavi Sachdev,
Technology Research News
Imagine a sensor in your car warning you
that your tire needs to be replaced soon. Now, imagine that the power
system for the sensor was made using something that resembles what you
wrapped your leftovers in - metal foil.
Researchers at the Dresden University of Technology in Germany have found
a way to make tiny thermoelectric generators using copper foil as a template.
The result is a cheap, flexible and recyclable generator that converts
environmental heat into electricity.
The key to the process is using the copper foil template rather than silicon
coated with a thin film of metal. The foil is cheaper, and using it as
both the substrate - the base of any integrated circuit - and the seed
layer - where the semiconductor crystals are grown - makes for a less
complicated fabrication process.
Using copper foil precludes having a dedicated sacrificial layer that
would have to be etched away, said researcher Wenmin Qu, a senior engineer
for microsensors and microsystems at the Hydac Group in Germany.
The microsystem could use the heat produced in the axles of cars and trains
by the motion of the wheels to detect damage inside the wheels or the
axles, said Qu. “Ideal microsystems should be intelligent and self-powered,”
he said.
Because the human body is a source of heat, someday, implanted medical
microdevices could also be powered with a thermoelectric generator that
operates on the body’s waste heat, said Qu.
“This generator could also be used in [the] reverse direction…as a cooling
element,” for computer chips and other electrical devices, he said. Applying
electrical power to the generator cools it, he explained.
The generator, which is as flexible as copper wire, comprises 100 pairs
of antimony-bismuth strips connected thermally and electrically. The entire
module measures 16 by 20 millimeters square, or about the size of a thumbtack.
Each strip in the module is about 10 microns high, 40 microns wide and
20 mm long.
The researchers made the generator by patterning the copper foil using
photolithography, then electrodpositing antimony and bismuth on the pattern.
They then added an epoxy film to the antimony-bismuth strips and hardened
it using ultraviolet light. “In the last step, the initial copper sheet
is entirely etched away, resulting in the antimony-bismuth strips being
embedded in the epoxy film,” said Qu.
The next step for Qu and his colleagues is designing a more efficient
thermoelectric generator based on bismuth telluride, he said.
The antimony-bismuth module can generate 250 millivolts, or a quarter
of a volt when the temperature difference between the ends is 30 degrees
celsius, said Qu. The bismuth telluride version could provide five times
the power of the antimony bismuth model, he said.
“Theoretically, the module with bismuth telluride will provide a voltage
of about 1.6 volts at a temperature difference of 30 degrees [celsius].
The real value could be a little lower than [1.6 volts]. However, we believe
it would not be lower than 1.2 volts,” said Qu.
The researchers are also looking into using titanium as a substrate instead
of copper foil, even though it is more expensive; in experiments, titanium
did not contaminate either antimony or bismuth layers, while the researchers
found small traces of copper contaminating the electrodeposited antimony
layer.
They hope to have a functional, equally flexible bismuth telluride module
within 2 to 3 years, according to Qu.
“There are a host of possible applications in microsystems of autonomous
electrical power sources that can run on low-temperature waste heat,”
said Yogendra Joshi, a professor of mechanical engineering at the University
of Maryland. “The key challenge is the ability to generate decent amounts
of power and the ability to integrate the device with the rest of the
microsystem,” he said.
“The authors have shown success in doing this with [antimony-bismuth]
micro thermocouples, with modest electrical power generation,” said Joshi.
Qu's research colleagues were Matthias Plötner and Wolf-Joachim Fischer
of the Dresden University of Technology. They published the research in
the Journal of Micromechanics and Microengineering, March 2001. The research
was funded by the Association of Industrial Research Organisations (AiF)
in Germany.
Timeline: 2 - 3 years
Funding: Institute
TRN Categories: Microelectromechanical Systems (MEMS)
Story Type: News
Related Elements: Technical paper, "Microfabrication of
thermoelectric generators on flexible foil substrates as a power source
for autonomous microsystems" in the Journal of Micromechanics and Microengineering,
March 2001, 146-152
Advertisements:
|
May
16, 2001
Page
One
Rough tools smooth design
Tightening
photonic bonds strengthens security
Tunable
superconductor makes better circuits
Flexible film turns
heat to power
Natural force
drives molecular ratchet
News:
Research News Roundup
Research Watch blog
Features:
View from the High Ground Q&A
How It Works
RSS Feeds:
News | Blog
| Books 
Ad links:
Buy an ad link
Advertisements:
|
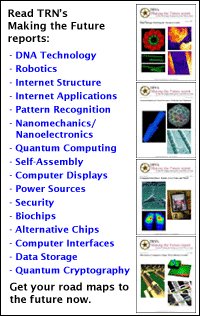
|
|
|