Flexible sensors make robot
skin
By
Eric Smalley,
Technology Research News
Skin
is very useful. In addition to neatly separating self from other, it provides
all kinds of feedback.
Researchers from the University of Tokyo have devised pressure-sensor
arrays that promise to give objects like rugs and robots the equivalent
of one aspect of skin -- pressure sensitivity.
The researchers' pressure sensor arrays are built from inexpensive
organic, or plastic, transistors on a flexible material. This allows for
dense arrays that can be used over large areas.
The arrays could be used in pressure-sensitive coverings in hospitals,
homes, gyms and cars to monitor people's health and performance, and eventually
as skin that would give robots the means to interact more sensitively with
their surroundings, said Takao Someya, an associate professor of electrical
engineering at the University of Tokyo.
The sensor skin works even when rolled around a cylinder as small
as 4 millimeters in diameter, said Someya. The researchers' prototype is
an eight-centimeter-square sheet containing a 32-by-32 array of organic
sensors -- a density of 16 sensors per square centimeter. In contrast, humans
have 1,500 pressure sensors per square centimeter in the fingertips, though
far fewer in most other places.
The pressure sensor arrays could be used in pressure carpets that
distinguish family members from strangers or sense when a hospital patient
collapses.
The active-matrix design allows the arrays to be smart enough to
enable specific sensors at certain feedback points to, for instance, monitor
the heart and breathing rate of a hospital patient who has fallen to the
floor, said Someya. The skin could measure whether an elderly patient is
just taking a rest, or needs help, he said.
Because organic transistor-based electronics are potentially very
cheap, "it is not unrealistic to spread pressure carpets all over the floor
in your house," said Someya.
The skin could also be used in car seats to monitor drivers' mental
and physical conditions, Someya said. "Our large-area pressure [sensing
abilities] would be helpful" in obtaining information through drivers seats,
he said.
The skin could eventually be used to make domestic robots more appropriately
sensitive of their surroundings, said Someya. "Robots working at home definitely
require touch sensitivity," said Someya. This has proven difficult, he said.
"It is not trivial matter to give a robot the ability to pick up an egg."
A pressure-sensitive skin would be helpful in making robots that
are capable of gently lifting a person or avoiding injuring people, said
Someya.
The prototype's pressure-sensitive rubber layer contains electrically
conductive graphite particles that change the layer's electrical resistance
when pressure is applied. This half-millimeter-thick layer and a copper
electrode are laminated to an array of organic transistors. Because the
pressure-sensitive layer and the electrode are unpatterned, only the transistor
assembly requires alignment, making the manufacturing process relatively
simple, according to Someya.
The sensors are controlled by an active matrix that uses a transistor
to record signals from each sensor in the array. The active matrix means
that only one transistor is on for each stimulated sensor, which allows
for lower power consumption and greater control than simpler pressure sensor
arrays that wire sensors together in grids. This makes the pressure-sensitive
skin appropriate for large-area sensor arrays, according to Someya.
Organic transistors are considerably larger and slower than the
silicon transistors used in most electronics, but they are also very cheap
-- they can be manufactured using a printing process. Many groups of researchers
are working to make speedier versions of organic transistors. The pressure-sensitive
skin, however, is an appropriate application for today's relatively large
and slow versions, said Someya.
There is work to be done before the pressure-sensitive skin is ready
for practical use, said Someya. The main challenge is making the organic
transistors more reliable, he said. The electrical characteristics of organic
transistors change in a matter of days, said Someya. To be practical, however,
organic transistors should be stable for years, he said.
Electronic skin could be ready for practical use in four to five
years, said Someya.
Takao Someya's research colleagues were Tsuyoshi Sekitani, Shingo
Iba, Yusaku Kato, Hiroshi Kawaguci, and Takayasu Sakurai. The work appeared
in the July 6, 2004 issue of the Proceedings of the National Academy
of Sciences (PNAS). The research was funded by the Japanese New Energy
and Industrial Technology Development Organization (NEDO), the Japanese
Ministry of Public Management, Home Affairs, Posts and Telecommunications,
and the Japanese Ministry of Education, Culture, Sports, Science and Technology.
Timeline: 4-5 years
Funding: Government
TRN Categories: Sensors; Robotics; Materials Science and
Engineering
Story Type: News
Related Elements: Technical paper, "A Large-Area, Flexible
Pressure Sensor Matrix with Organic Field-Effect Transistors for Artificial
Skin Applications," Proceedings of the National Academy of Sciences, July
6, 2004
Advertisements:
|
September 22/29, 2004
Page
One
Fuel cell converts
waste to power
Bank transfer demos
quantum crypto
Agent model yields leadership
Flexible sensors
make robot skin
Briefs:
Microscope
etches ultrathin lines
Nanowire makes
standup transistor
Plastics ease
nanotube circuits
Virus forms nano template
Photo molecules
flip current
Nanotubes
on cloth fire electrons
News:
Research News Roundup
Research Watch blog
Features:
View from the High Ground Q&A
How It Works
RSS Feeds:
News | Blog
| Books 
Ad links:
Buy an ad link
Advertisements:
|
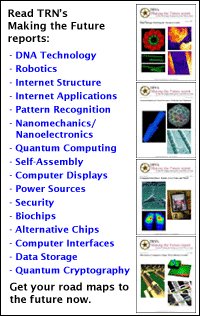
|
|
|