Process
promises better LCD production
By
Chhavi Sachdev ,
Technology Research News
The liquid crystal displays in your laptop
screen and your cell phone were probably made using a process called rubbing
that is almost a century old. The reason rubbing has prevailed is not
because it is the best method -- indeed, there are many drawbacks to implementing
it -- but because there has never been a viable substitute that could
be used for large-scale manufacturing.
Researchers at IBM have endeavored to address the display industry’s complaints
by developing a cheaper, easier, higher-yield non-contact technique for
aligning the liquid crystals.
In the process of rubbing, a giant roller wrapped in velvet is rubbed
on a polymer surface that has been baked in a furnace. Liquid crystal
molecules on the surface align themselves in the direction of the motion.
The new process, in contrast, does not make any contact with the surface.
Atoms shot from an ion gun to the surface knock out all but those molecules
that oriented in the same direction the ions are traveling, said Praveen
Chaudhari, a scientist at IBM and the lead researcher of the project.
The biggest limitation of the rubbing technique is that it introduces
debris. To keep fibers from the rubbing cloth out of other manufacturing
processes, the rubbing machine must be placed in a separate clean-room
environment.
The technique is also somewhat unreliable because the rollers can degrade
unevenly, causing defects that may go undetected until hundreds of displays
have been manufactured. Rubbing can leave streaks which degrade image
quality and can produce an electrostatic discharge that affects the circuitry
of the display. Replacing the rubbing cloth also delays production.
The idea behind the non-contact alignment method is simple, according
to Chaudhari. An ion beam is fired at diamond-like carbon and the angle
of the beam determines the alignment of the liquid crystal molecules.
Atoms in diamond-like carbon are interconnected in a network that has
no order. “The random network has rings of atoms in it. A given ring can
be described by a plane,” explained Chaudhari. A perpendicular ion beam,
therefore, "tends to have a higher probability of knocking [perpendicular]
atoms out, than if the plane is parallel to [it]" he said.
"What you're left with after you keep shooting atoms are those planes
that are parallel to the ion beam. All the ones that are perpendicular
are destroyed. It's like a Darwinian process of selection. The liquid
crystals align themselves along [the surviving planes] and you're done,"
said Chaudhari.
The researchers replaced the baked polymer surface with a layer of diamond-like
carbon film vapor-deposited on a substrate. Diamond-like carbon is widely
used in the electronics industry, and therefore readily available. The
low energy ion gun that replaced the rubbing roller is also commercially
available. "So the tools and manufacturing experience already existed,"
said Chaudhari.
The result is a debris-free, reliable, cost-effective, highly scalable,
and more environmentally friendly method than the one currently in use,
according to Chaudhari. IBM used the process to make a prototype LCD,
"Bertha," that measures 22 inches and has 3,840 by 2,400 pixels.
"The technique is certainly novel," said Satyendra Kumar, a professor
of physics and chemical physics at Kent State University. "Although they
have demonstrated in their laboratory it works very well, I have my reservations
about its implementation on an assembly line. Basically, each plate will
have to be put in a vacuum and bombarded by ions. This hardly appears
more convenient or low cost than rubbing," he said. "Other techniques,
such as UV exposure, appear far more attractive and practical," he added.
No other rubbing technique has been used to demonstrate a large display
area, but the IBM researchers "have already demonstrated a working large
area LCD using this technique," said N. V. Madhusudana, a professor at
the Raman Research Institute in Bangalore, India. He also pointed out,
however, that the IBM technique would require additional vacuum lines
to process the displays.
IBM has established a pilot assembly line, Chaudhari said. The researchers
expect large-scale production of the LCD's by the end of 2001.
The research was published in the May 3, 2001 issue of the journal Nature
and prototypes of the display were shown at the Society of Information
Display meeting in June, 2001. The research was funded by IBM.
Chaudhari's colleagues were James Lacey, James Doyle, Eileen Galligan,
Shui-Chi Alan Lien, Alesandro Callegari, Gareth Hougham, Norton D. Lang,
Paul S. Andry, Richard John, Kei-Hsuing Yang, Minhua Lu, Chen Cai, James
Speidell, Sampath Purushothaman, John Ritsko, Mahesh Samant, Joachim Stöhr,
Yoshiki Nakagawa, Yoshimine Katoh, Yukito Saitoh, Kazumi Sakai, Hiroyuki
Satoh, Shuichi Odahara, Hiroki Nakano, Johji Nakagaki & Yasuhiko Shiota
at IBM research.
Timeline: now
Funding: corporate
TRN Categories: Materials Science and Engineering
Story Type: News
Related Elements: Technical paper, "Atomic-beam alignment
of inorganic materials for liquid-crystal displays," Nature, May 3, 2001.
Advertisements:
|
June
13/20, 2001
Page
One
Stressed silicon goes
faster
Artificial
synapses copy brain dynamics
DNA device detects
light signals
Lightwaves
channel atoms to make chips
Process promises
better LCD production
News:
Research News Roundup
Research Watch blog
Features:
View from the High Ground Q&A
How It Works
RSS Feeds:
News | Blog
| Books 
Ad links:
Buy an ad link
Advertisements:
|
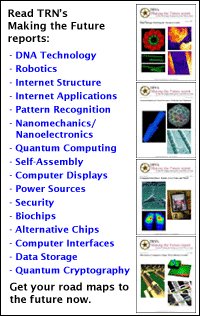
|
|
|