T-shirt
technique turns out flat screens
By
Kimberly Patch,
Technology Research News
The current technique for spreading light-emitting
polymers on glass to make passive matrix computer screens is wasteful,
according to researchers from Siemens Corporation in Germany. It's also
not something you want to try with a screen surface the size of a wall
or billboard.
Spin-coating, which uses centrifugal force to spread polymers on a surface
that's spinning 2000 times per minute, results in a nice even coat of
the polymer diodes that light up an organic light emitting diode (OLED)
computer display. But it's a messy business.
Somewhere between 5 and 10 percent of the polymer actually ends up on
the surface; the other 90 to 95 percent either flies off during the process
or ends up in the works, said Georg Wittmann, project manager for the
OLED project at Siemens.
In addition, it becomes more difficult to use spin coating as the screen
size gets larger, said Wittmann. "The larger [the surface] the more difficult
it is to coat the outer areas of the glass," he said.
The researchers modified an existing printing process to provide an alternative
way to spread polymers on large surfaces. Screen printing, which guides
inks onto a surface through fine mesh, is an order of magnitude less wasteful
than spin coating. "We use 80 or 90 percent," of the polymers, said Wittmann.
The process has the potential to produce relatively inexpensive computer screens
large enough to cover a wall or billboard. The catch is the researchers'
modified printing process cannot print the polymers in as fine a resolution
as they can be spun. This means the printing technique is only appropriate
for fairly large screens. In addition, although the process allows for
different colors to be printed in different places on the screen, the
resolution is not high enough to produce full-color screens that can make
any color appear anywhere on the screen.
Screen printing is an established process used not only to guide heavy
inks onto T-shirts, but also to lay down electric conducting pastes on
printed circuit boards.
The catch to adapting screen printing for making computer displays was
the viscosity of the polymer the researchers need to print on the glass
part of a computer screen. "The tricky part is the emitting layer in this
screen printing technique is extremely low viscosity... we managed to
develop a process that we can use with very low viscous printing solution,"
Wittmann said.
The viscosity of water, for instance, is 1 millipascal seconds, while
the viscosity of the pastes traditionally used in screen printing are
much higher -- more like 1,000 or 2,000 millipascal seconds, Wittmann
said. The OLE polymer is much more like water than paste, with a viscosity
of 10 to 20 millipascal seconds, he said. "It's almost water-like. You
wouldn't be able to distinguish it [by] feel."
The idea is a "fresh and useful manufacturing approach for large-area
polymer OLED displays," said David Braun, an associate professor of electrical
engineering at California Polytechnic State University in San Luis Obispo.
Although the idea is not novel because silk screening T-shirt designs
is well-established, the research is important because "screen printed
displays work, perhaps better than one might have predicted," Braun said.
"The simple printing technique allows people to make relatively complex
electronic devices. It's potentially useful for printing large area...
displays [and] I suspect that there are some cost advantages," he said.
The research could help polymer OLED displays to gain wider acceptance
of the market in the next few years, Braun added.
The researchers are working spreading the polymers more evenly, making
the edges where the ink ends sharper, and improving the resolution, said
Wittmann. The current process can print a spot of polymer, or pixel, 300
microns away from the next one. Spin coating can achieve a resolution
an order of magnitude better, with pixels separated by only 20 or 30 microns,
he said.
Wittmann's research colleagues were Jan Birnstock, Jörg Blässing, Arvid
Hunze Matthias Stößel, Karsten Heuser and J. Wörle from Siemens in Germany,
and Albrecht Winnacker of Erlangen-Nürnberg University in Germany. They
published the research in the June 11, 2001 issue of Applied Physics Letters.
The research was funded by OSRAM GmbH.
Timeline: Now
Funding: Corporate
TRN Categories: Materials Science and Engineering
Story Type: News
Related Elements: Technical paper, "Screen-Printed Passive
Matrix Displays based on Light-Emitting Polymers," Applied Physics Letters,
June 11, 2001.
Advertisements:
|
July
25, 2001
Page
One
Sounds attract camera
Interface lets
you point and speak
Quantum logic counts
on geometry
T-shirt technique
turns out flat screens
Rating systems
put privacy at risk
News:
Research News Roundup
Research Watch blog
Features:
View from the High Ground Q&A
How It Works
RSS Feeds:
News | Blog
| Books 
Ad links:
Buy an ad link
Advertisements:
|
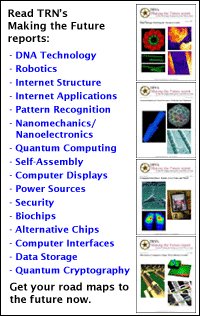
|
|
|