Hitting
the deck cools microdevices
By
Eric Smalley,
Technology Research News
It doesn't take a lot to overheat microscopic
mechanical components like the tiny flakes of metal and semiconductor
used in microelectromechanical systems.
And if these bits of material are moving parts mounted above the surface
of the chip, the only way they can cool off is to wait for the excess
heat to dissipate through the air, which is not a good thermal conductor.
Researchers at the University of Minnesota have developed a technique
for cooling these components that is the equivalent of a blacksmith periodically
plunging red hot iron into a bucket of water.
"If you have a microdevice, say a MEMS-type
device... you can change its thermal conductivity by placing it in contact
with its underlying substrate," said Joseph J. Talghader, an assistant
professor of electrical and computer engineering at the University of
Minnesota.
The method can be used to finely control the temperature of these devices.
"Not only can you quench it, but you can actively control the thermal
dissipation speed of [the device] by periodically placing it in and out
of contact with the substrate," Talghader said.
The researchers have built a series of microdevices made up of movable
filaments of titanium-coated silicon mounted above a surface of the same
material. The .75-micron-thick filaments range from 50 to 450 microns
long and 6 to 20 microns wide. There are 1,000 microns in a millimeter.
When a filament heats up, its electrical resistance changes. Electrical
resistance, or the ease with which electrons flow through a material,
is easily measured. The researchers rigged their device to apply a pulse
of electricity to the filament when it heated up enough to make its resistance
cross a certain threshold. The pulse slapped the filament down to the
surface, which rapidly drew heat from the filament.
The researchers were able to lower and raise the filaments much more rapidly
than the bits of metal-coated silicon heated. This allowed them to precisely
tune the filaments' thermal conductivity, or the rate at which the filament
can transfer heat. In theory, the conductivity could be set to any level
between the low conductivity in its raised position and the high conductivity
in its lowered position, said Talghader.
The technique could be used to protect the sensitive MEMS components of
thermal imagers, optical networking
equipment and chemical labs-on-a-chip.
Thermal imagers use an array of metal elements to translate infrared radiation
to electrical signals, which are then used to produce an image. Because
they are very sensitive, they are prone to thermal overload, said Talghader.
"These little MEMS elements that make up these [imagers] are designed
to be extremely, extremely sensitive, and so if you are looking at something
that is fairly dim and then all of the sudden something bright comes into
your field of view you can often blow out the element," he said.
Telecommunications
networks increasingly use arrays of tiny mirrors to direct the pulses
of light carried over fiber-optic cables. "[The mirrors] are little plates
of polysilicon with a sheet of metal on them. They're very thermally isolated
and so they're very sensitive to the light that [hits] them," said Talghader.
And in the emerging field of microchemical systems, MEMS devices are used
to mix tiny amounts of chemicals. Sometimes the resulting reactions produce
sudden bursts of heat that can damage the devices, said Talghader.
"This is a new approach that has not been demonstrated before," said Yu-Chong
Tai, a professor of electrical engineering at the California Institute
of Technology. "The approach is sound and results are plausible."
"However, I... could not come up with some killer application for it,"
he said. "There are many interesting applications such as [infrared] imagers
that will require the best thermal isolation one can get. Maybe what this
approach can do is to provide tuning for each and every IR detector so
the uniformity is better."
The method could be used in thermal imagers in three years, said Talghader.
Practical applications for microchemical systems are probably 10 years
away, he said.
Talghader's research colleague was Ryan N. Supino. They published the
research in the March 19, 2001 issue of Applied Physics Letters. The research
was funded by the Defense Advanced Research Projects Agency (DARPA).
Timeline: 3 years, 10 years
Funding: Government
TRN Categories: Microelectromechanical Systems (MEMS)
Story Type: News
Related Elements: Technical paper, "Electrostatic Control
of Microstructure Thermal Conductivity," Applied Physics Letters, March
19, 2001
Advertisements:
|
March
28/April 4, 2001
Page
One
Programming goes quantum
Diversity trumps fitness
Nanotubes paint clear
picture
Hitting the deck
cools microdevices
Magnetic fields move
microbeads
News:
Research News Roundup
Research Watch blog
Features:
View from the High Ground Q&A
How It Works
RSS Feeds:
News | Blog
| Books 
Ad links:
Buy an ad link
Advertisements:
|
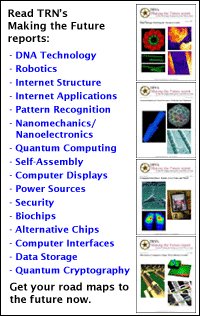
|
|
|